Title
Quality Management
Quality management systems aim to consistently provide products or services that satisfy customer, statutory or regulatory requirements. Both statutory requirements and regulatory requirements are those that are required by law. Statutory refers to laws passed by a state or central government, while regulatory refers to regulations issued by a regulatory body appointed by a state.
And in another words, quality management system is a systemic view of the organization from the perspective of how it creates and retains customers. Usually the quality management system is embedded in the operating management system. We usually understand the quality management system in a much broader way, we don’t want only to satisfy the customers and regulators, we also want to satisfy or at least balance other stakeholders’ requirements. We shouldn’t forget about our employees, shareholders, or our community. As other systems in organizations, quality system is a subsystem to an operating system. We define a system is an interaction of elements within a defined boundary producing outputs greater than the sum its parts.
When developing a management system or an operating system of the business, you should have in mind the cycle of sustained success. You start considering the circle with the strategic intent which is your vision (what would you like to be in 5-10 years), your purpose (your overriding, independent from your products and services, reason for existing) and your mission (what you need to be doing now to achieve your vision in the future). These drive the need to organize people and objects in order to realise the strategic intent. We need to put in place structures, processes, procedures, roles, leadership approaches, projects and systems. We use for that purpose general goals with more specific objectives, usually a few to each goal. If the organization is well established and sustained for a longer time, it delivers results in performance, products and services and these satisfy stakeholders: customers, employees, regulators, community, etc. Stakeholders influence your strategic intent causing it to be modified and improved.
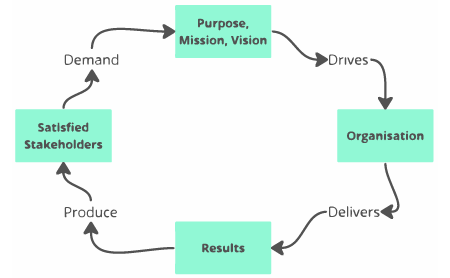
So, how do you go about installing a quality management system? Well in order to do that you should proceed by establishing, implementing, maintaining and improving the quality system. You should change the organization in such a way that the model of sustained success becomes a reality. First of all you establish the system by drawing it up, then you implement it by embedding it the current working systems. After implementation we need to constantly supervise our system in order not to make it deteriorate when our attention is diverted away from that. The last thing is we need to improve our system, because just maintaining is not enough to make it effective and efficient. We need to continually make it better. Apart from the quality systems we also have to improve our product and services on regular basis. Let’s get back once again to the requirements. They might be expected or not expected needs or wants that are stated, generally implied or obligatory. A need will regard to something we must have or experience to survive or to a function in the product that has to be there to make it work properly. We may be aware of the expected needs and unaware of unexpected needs e.g. a fuel pump in our car. We are able to survive without ice cream, that’s our want. The local government might enforce some laws for the process of ice cream production be safe from the public health point of view – that will be an obligatory want. It is also generally implied want for the ice cream to be safe and tasty. And the stated want might be the verbal requirement for the ice cream to be of strawberry flavour. Some of the requirements might come in terms of objectives and some in terms of constraints: what we want to do or what we can’t do. The following principles from “ISO 9000 Quality Systems Handbook” by David Hole can become a useful tool to quickly conduct an audit or build a performance evaluation tool determining the condition of our quality management. The first principle called customer focus checks the following: our understanding of customer needs and expectations and meeting customer requirements in a way that meets the needs and expectations of all other stakeholders, our sensitivity to their preferences; the communication of these needs and expectations throughout the organization; our knowledge, skills and resources to satisfy customers, measurement of their satisfaction and our acting on results; our understanding and management of customer relationship and whether we relate our objectives directly to customers needs and wants. The second principle called leadership checks the following: the fact of establishing and communicating a clear vision of the future, values and ethical role models; whether we are proactive and lead by example; our understanding and responding to changes in the external environment; considering the needs and wants of all stakeholders; whether we build trust and eliminate fear and provide people with required resources and freedom to act with responsibility and accountability; whether we promote open and honest communication and educate, train and coach people; whether we set challenging goals aligned with the mission and vision; whether we communicate and implement a strategy to achieve these goals; whether we use performance measures that encourage behaviour consistent with these goals. The third principle called engagement of people checks the following: whether we feel personally and emotionally connected to the organization; whether we feel pride in recommending it as a good place to work for other people; whether you feel a close attachment to the values, ethics and actions of the organization. The fourth principle process approach checks the following: whether we know objectives to achieve and the process that will enable it; whether we know what measures will indicate the achieved objectives; whether we have clear responsibility, authority and accountability for the results; whether we can assess risk before taking action and act in a way that mitigates the impact of the risks; whether we know what resources, information and competences are required to achieve the objective; whether we understand how the outputs of one process affect the outputs of other processes; whether we can find better ways of achieving process objectives and improving process efficiency; whether we can regularly confirm that the objectives remain relevant to the needs of the organization. The fifth principle called systems approach checks the following: whether we are able to visualize the organization as a system of interdependent elements; whether we understand that time delays and the chain effects of actions often mask the connection between cause and effect; whether we don’t lose sight of the whole when dealing with the detail. The sixth principle called improvement checks the following: whether we as an individual in the organization improve products, services, processes and systems; whether we apply the basic improvement concepts of incremental improvement and breakthrough improvement; whether we use periodic assessments against established criteria of excellence to identify areas for potential improvement; whether we continually improve the efficiency and effectiveness of all processes; whether we promote prevention-based activities; whether we provide every member of the organization with appropriate education and training on the methods and tools of continual improvement; whether we establish measures and goals to guide and track improvements; whether we recognize improvement. The seventh principle called evidence-based decision-making checks the following: whether we define performance measures that relate to the quality characteristics required for the process, product or service being measured; whether we take measurements relevant to the product or process objectives; whether we ensure that the data and information are sufficiently accurate, reliable and accessible; whether we analyse the data and information using valid methods; whether we understand the value of statistical techniques; whether we make decisions and take action based on the results of logical analysis balance with experience and intuition. The eighth principle relationship management checks the following: whether we understand which interested parties the organization depends on and which may threaten its success; whether we jointly establish clear understanding of the needs and expectations of those parties; whether we endeavour to mitigate the effect of those parties that threaten its success; whether we establish relationship that balance short term gains with long term considerations for the organization and society; whether we create clear and open communication; whether we initiate joint development and improvement of products, services and processes; whether we share information and future plans where it’s beneficial for the organization; whether we recognize improvements and achievements with those interested parties that have contributed to the organization’s success. Quality management is about constantly improving quality of products and one of the most popular methods to do it is a PDCA (PDSA) cycle or when we want to stress the need of evaluation E-PDCA. This tool helps improve products, services and organizational processes. While you repeat the PDCA loops you get closer to either reach you improvement goal or you learn valuable lessons to reach them with the next cycle. First step is to Evaluate the situation, what is actually happening, what should be happening, what must be happening and what is the ideal condition (this is part of the Context of the Organization ISO 9001 clause). Second step is called Plan. It determines what needs to be changed (objectives), it plans what is to be done in order to satisfy the objectives, in what sequence, when it needs to be done, who is to be involved and what resources will be required, in other words: the schedule, processes and responsibilities (this is part of the Planning ISO 9001 clause). And remember we are talking here about small, quick, incremental solutions in improvement projects. So far we have done situation assessment, objectives and a plan. Now we make the plan happen by making the next step called Do, which is the implementation on a small, trial scale with minimal disruption to your business. We cascade down our plan into specific departments and individuals, we acquire resources, train people and verify that the plan is being implemented as intended (this is part of the Support and Operation ISO 9001 clauses). The third step called Check or Study. Analyse the results from the previous stage and compare them with the desired ones. We check and study what we’d learnt and establish whether the predicted results were achieved. In observing the results of a planned change some things may have gone right and other things gone wrong. From this we can learn but only if we discover why things worked out the way they did. This is important to know so that we may not only avoid the failures but repeat the success in the future (this is part of the Performance Evaluation ISO 9001 clause). If the solution implemented on a small scale failed than you return to the first step: Evaluate or second: Do. If you succeeded progress to the next step. The last step named Act or more precisely Amend. Depending on the results of the change: if they bring improvement, we roll out the change in policies throughout organization, if not, we review the objective and the plan, we find better solutions and repeat E-PDCA cycle (this is part of the Improvement ISO 9001 clause).
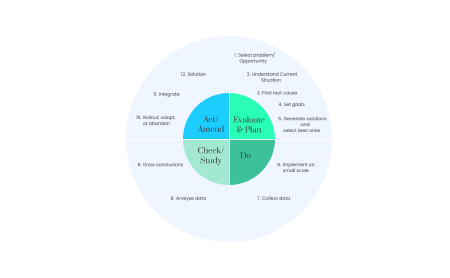
So how we go about making the Quality Management System work in our business? There are 4 phases to help us do it in an orderly and efficient way: Establishment of the system, Implementing the system, Maintaining the system and Improving the quality system. In the first phase we approach the organization from a systems perspective and we put a boundary around the elements that through their interactions create and retain customers, and put all other elements outside the controlled system. We map the processes and create a library for them. We create a model with systems maps, process maps, activity sequence diagrams and organization charts. You can also include the key issues from the SWOT analysis relative to the processes. Second phase is implementing the quality system. We put into effect any new policies and practices and introduce change management methods. The most important elements of this change include: obtain the management and employee commitment, appoint the right leader, establish clear rule for communication, prioritize action, follow the plan and track progress, take responsibility, coordinate, allow sufficient time, deal with the resistance to change, educate and train the staff affected by the change and recognize which goals are unrealistic. Third phase – managing a quality management system – is key, because any system without maintenance will deteriorate. In maintaining the QMS you will need to keep correcting special causes of variations, keep physical resources operational, keep the personnel competent (capable: knowledge, skills and having resources: tangible assets, intangible assets and human assets) keep financial resources ready to replenish consumables, worn out or obsolete equipment, keep the documented information up to date, keep space available to accommodate input and output, keep buildings, land and offices clean and tidy, remove the waste and keep benchmarking processes against best in the field. The last, fourth phase deals with continually improving the quality system. This means that we have to be putting into effect changes made to the model on a recurring basis to enhance the performance of the organization. We should understand that we must improve not only the effectiveness of the quality system, but also the quality of our products and services. We should also mention that as the continual improvement is important, the discontinuous improvement is at least same important or more. The discontinuous improvement is tantamount to creativity and transformation. Continual improvement of the QMS is specifically focused on the attributes of suitability, adequacy and effectiveness. Continually improving suitability (being right and correct for a particular situation or person) means gradually improving the extent to which the QMS fits the organization's purpose. Continually improving adequacy means gradually improving the extent to which the QMS is sufficient (enough) in meeting the applicable requirements. Continually improving effectiveness (successful in something you want to do) means gradually improving the extent to which planned activities are realised and planned results achieved. Apart from the continuous improvement method, quality management is based on a process approach. The process is anything that can be described by a verb ending in -ing with preferably an object, for example, ‘making bread’. Apart from continuously improving products or services, the business has to improve their internal processes to achieve cost reductions and more job satisfaction for the employees. If a process is needed to achieve an objective, we need to resource it and make it operational. We also know that processes require activation, that is, an event that triggers them into operation. To ensure that a predetermined process is run when the event that would activate it occurs, people need to respond to that event. And that to happen they need to be aware that a process has been designed for such an event. This is where a role of process maps and process libraries applies. They show relationships between the processes, inputs and outputs and further description. It might be useful when running a business operation optimization to determine all most important processes by mapping them. Such processes need to be easily accessible by establishing process libraries. When mapping processes it’s good to establish: the activators: input, event or time; the inputs: work instruction, raw material, tool, measuring method, measuring device, protection, feedback; and outputs: plan, activity record, waste, noise, measurement record, conforming item, nonconforming item, feedback. Outputs are direct effects produced by a process and further on we encounter outcomes i.e. indirect effects of a process having effects upon other stakeholders. Take into consideration that there are 4 core business processes: mission management, resource management, demand creation and demand fulfilment. Mission management process determined the purpose, mission and direction (strategy) of the businesses, continually confirms that the business is proceeding in the right direction and makes course corrections to keep the business focused on its mission. The business processes are developed within mission management as the enabling mechanism by which the mission is accomplished. Resource management process specifies, acquires and maintains the resources required by the business to fulfil the mission and disposes off any resources that are no longer required. Demand creation process identifies new technologies, new markets, unsatisfied customer needs and exploits markets with products and services and a promotional strategy that influences decision makers and attracts potential customers to the organization. New product and service development would form part of this process if the business were market driven. Demand fulfilment process converts customer requirements into products and services in a manner that satisfies all stakeholders. New product development would form part of this process if the business were order driven (the order contained performance requirements for which a new product or service had to be designed). Each of these processes comprise of further work processes, work processes comprise of activities and activities comprise of tasks. Here are more detailed examples of work processes or activities that are grouped in the following way: Managing mission: scan external environment, establish vision & mission, develop org structure, identify strategic issues, manage enterprise risk, develop capability, establish goals, develop strategy, measure performance, manage PR; Managing resources: develop HR strategy, plan human resources, manage IT, manage finance, recruit employees, deploy resources, manage assets, maintain buildings, maintain equipment, manage employee relations; Creating the demand: understand markets, plan product development, develop marketing strategy, advertise product, test market, develop product, build prototypes, receive enquiries, accept orders; Fulfilling the demand: plan production/service, select suppliers, develop production process, produce product, procure materials/services, pack product, assemble & test product, deliver product/service, manage logistics, support customer.
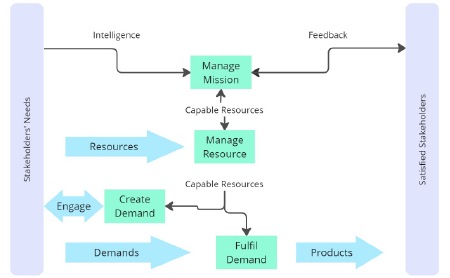
When we undertake work we do it for a reason (past) and to achieve some objective (future). We acquire the things we need to achieve the objective; there is a series of actions we take; tools, equipment and information we use; energy and materials we consume; and decisions we make from the beginning to the end. These are variables. The work progresses until completion. This progression is a process; it has a beginning and an end. It begins with an event or when we receive a command or reach a date and ends when we are satisfied with the resultant output. This output might be a tangible product or a service we provide to someone else. The output will possess certain features or characteristics, some of them needed, some of them not needed.
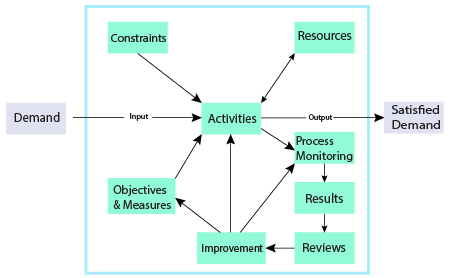
Measures (in the diagram above) are performance measures such as metrics to determine if a target objectives and goals are being met, i.e. productivity, profit margin, cost.
There are 7 aspects of the ISO 9000 quality management standard: Context of organization, Leadership, Planning, Support, Operation, Performance evaluation and Improvement. In the first aspect called the Context, we focus on our external and internal environment, we try to understand our organization, understand the needs and expectations of interested parties, determine the scope of our quality management system and its processes. In the Leadership aspect we try to understand the leadership quality and commitment, we draw up the quality policy, determine organizational roles, responsibilities and authorities and focus on customer. In the Planning aspect of the standard we plan actions to address risks and opportunities; and we set up quality objectives. In the Support aspect we analyse all crucial elements to achieve high quality such as: people, infrastructure, environment for processes, monitoring, measuring resources, organizational knowledge, competence, awareness, communication and documented information. In the next aspect of the quality standard the Operation, we deal with the operations management area concerned with designing and controlling the processes of designing and producing products and designing and providing services. It covers the demand fulfilment process with interfaces to demand creation, resource management and mission management. The Performance Evaluation aspect deals with monitoring, measurement, analysis and evaluation, customer satisfaction and management review. And the last aspect of the quality management standard the Improvement helps to determine and select opportunities for improvement, deals with nonconformity, corrective actions and continual improvement of the quality management system. For an organization to achieve its vision it needs constancy of purpose, and the quality policy is one such artefact to create constancy of purpose relative to quality. To quickly assess the state of your approach to quality ask your company these quality questions: Do customer receive defective products even if they will accept them? Do employees put quality first and consequently potentially stop the production line? Is it an environment where employees hide their mistakes or freely own up to them? Is it an environment where employees walk by problems they find or alert the area supervisor? Do employees meet targets changed to align with the process’s assessed capability? Are downstream processes to compensate for the poor quality provided by upstream processes? Do employees tolerate poor performance of materials, equipment, facilities, processes, people or initiate improvement? Quality management system when properly implemented and audited by a certification body can become a very good reputation enhancer and in itself it can motivate staff to be more creative and productive.
Fit for purpose output and processes
Quality Management
Quality management systems aim to consistently provide products or services that satisfy customer, statutory or regulatory requirements. Both statutory requirements and regulatory requirements are those that are required by law. Statutory refers to laws passed by a state or central government, while regulatory refers to regulations issued by a regulatory body appointed by a state.
And in another words, quality management system is a systemic view of the organization from the perspective of how it creates and retains customers.
Usually the quality management system is embedded in the operating management system. We usually understand the quality management system in a much broader way, we don’t want only to satisfy the customers and regulators, we also want to satisfy or at least balance other stakeholders’ requirements. We shouldn’t forget about our employees, shareholders, or our community.
As other systems in organizations, quality system is a subsystem to an operating system. We define a system is an interaction of elements within a defined boundary producing outputs greater than the sum its parts.
When developing a management system or an operating system of the business, you should have in mind the cycle of sustained success. You start considering the circle with the strategic intent which is your vision (what would you like to be in 5-10 years), your purpose (your overriding, independent from your products and services, reason for existing) and your mission (what you need to be doing now to achieve your vision in the future). These drive the need to organize people and objects in order to realise the strategic intent. We need to put in place structures, processes, procedures, roles, leadership approaches, projects and systems. We use for that purpose general goals with more specific objectives, usually a few to each goal. If the organization is well established and sustained for a longer time, it delivers results in performance, products and services and these satisfy stakeholders: customers, employees, regulators, community, etc. Stakeholders influence your strategic intent causing it to be modified and improved.
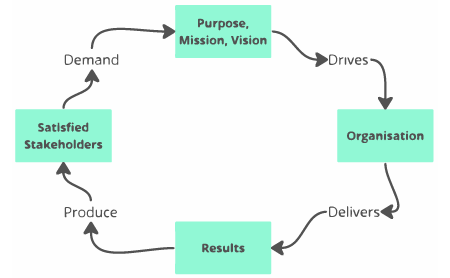
So, how do you go about installing a quality management system? Well in order to do that you should proceed by establishing, implementing, maintaining and improving the quality system. You should change the organization in such a way that the model of sustained success becomes a reality. First of all you establish the system by drawing it up, then you implement it by embedding it the current working systems. After implementation we need to constantly supervise our system in order not to make it deteriorate when our attention is diverted away from that. The last thing is we need to improve our system, because just maintaining is not enough to make it effective and efficient. We need to continually make it better.
Apart from the quality systems we also have to improve our product and services on regular basis.
Let’s get back once again to the requirements. They might be expected or not expected needs or wants that are stated, generally implied or obligatory. A need will regard to something we must have or experience to survive or to a function in the product that has to be there to make it work properly. We may be aware of the expected needs and unaware of unexpected needs e.g. a fuel pump in our car. We are able to survive without ice cream, that’s our want. The local government might enforce some laws for the process of ice cream production be safe from the public health point of view – that will be an obligatory want. It is also generally implied want for the ice cream to be safe and tasty. And the stated want might be the verbal requirement for the ice cream to be of strawberry flavour.
Some of the requirements might come in terms of objectives and some in terms of constraints: what we want to do or what we can’t do.
The following principles from “ISO 9000 Quality Systems Handbook” by David Hole can become a useful tool to quickly conduct an audit or build a performance evaluation tool determining the condition of our quality management.
The first principle called customer focus checks the following: our understanding of customer needs and expectations and meeting customer requirements in a way that meets the needs and expectations of all other stakeholders, our sensitivity to their preferences; the communication of these needs and expectations throughout the organization; our knowledge, skills and resources to satisfy customers, measurement of their satisfaction and our acting on results; our understanding and management of customer relationship and whether we relate our objectives directly to customers needs and wants.
The second principle called leadership checks the following: the fact of establishing and communicating a clear vision of the future, values and ethical role models; whether we are proactive and lead by example; our understanding and responding to changes in the external environment; considering the needs and wants of all stakeholders; whether we build trust and eliminate fear and provide people with required resources and freedom to act with responsibility and accountability; whether we promote open and honest communication and educate, train and coach people; whether we set challenging goals aligned with the mission and vision; whether we communicate and implement a strategy to achieve these goals; whether we use performance measures that encourage behaviour consistent with these goals.
The fourth principle process approach checks the following: whether we know objectives to achieve and the process that will enable it; whether we know what measures will indicate the achieved objectives; whether we have clear responsibility, authority and accountability for the results; whether we can assess risk before taking action and act in a way that mitigates the impact of the risks; whether we know what resources, information and competences are required to achieve the objective; whether we understand how the outputs of one process affect the outputs of other processes; whether we can find better ways of achieving process objectives and improving process efficiency; whether we can regularly confirm that the objectives remain relevant to the needs of the organization.
The fifth principle called systems approach checks the following: whether we are able to visualize the organization as a system of interdependent elements; whether we understand that time delays and the chain effects of actions often mask the connection between cause and effect; whether we don’t lose sight of the whole when dealing with the detail.
The sixth principle called improvement checks the following: whether we as an individual in the organization improve products, services, processes and systems; whether we apply the basic improvement concepts of incremental improvement and breakthrough improvement; whether we use periodic assessments against established criteria of excellence to identify areas for potential improvement; whether we continually improve the efficiency and effectiveness of all processes; whether we promote prevention-based activities; whether we provide every member of the organization with appropriate education and training on the methods and tools of continual improvement; whether we establish measures and goals to guide and track improvements; whether we recognize improvement.
The seventh principle called evidence-based decision-making checks the following: whether we define performance measures that relate to the quality characteristics required for the process, product or service being measured; whether we take measurements relevant to the product or process objectives; whether we ensure that the data and information are sufficiently accurate, reliable and accessible; whether we analyse the data and information using valid methods; whether we understand the value of statistical techniques; whether we make decisions and take action based on the results of logical analysis balance with experience and intuition.
The eighth principle relationship management checks the following: whether we understand which interested parties the organization depends on and which may threaten its success; whether we jointly establish clear understanding of the needs and expectations of those parties; whether we endeavour to mitigate the effect of those parties that threaten its success; whether we establish relationship that balance short term gains with long term considerations for the organization and society; whether we create clear and open communication; whether we initiate joint development and improvement of products, services and processes; whether we share information and future plans where it’s beneficial for the organization; whether we recognize improvements and achievements with those interested parties that have contributed to the organization’s success.
Quality management is about constantly improving quality of products and one of the most popular methods to do it is a PDCA (PDSA) cycle or when we want to stress the need of evaluation E-PDCA. This tool helps improve products, services and organizational processes. While you repeat the PDCA loops you get closer to either reach you improvement goal or you learn valuable lessons to reach them with the next cycle.
First step is to Evaluate the situation, what is actually happening, what should be happening, what must be happening and what is the ideal condition (this is part of the Context of the Organization ISO 9001 clause).
Second step is called Plan. It determines what needs to be changed (objectives), it plans what is to be done in order to satisfy the objectives, in what sequence, when it needs to be done, who is to be involved and what resources will be required, in other words: the schedule, processes and responsibilities (this is part of the Planning ISO 9001 clause). And remember we are talking here about small, quick, incremental solutions in improvement projects.
So far we have done situation assessment, objectives and a plan. Now we make the plan happen by making the next step called Do, which is the implementation on a small, trial scale with minimal disruption to your business. We cascade down our plan into specific departments and individuals, we acquire resources, train people and verify that the plan is being implemented as intended (this is part of the Support and Operation ISO 9001 clauses).
The third step called Check or Study. Analyse the results from the previous stage and compare them with the desired ones. We check and study what we’d learnt and establish whether the predicted results were achieved. In observing the results of a planned change some things may have gone right and other things gone wrong. From this we can learn but only if we discover why things worked out the way they did. This is important to know so that we may not only avoid the failures but repeat the success in the future (this is part of the Performance Evaluation ISO 9001 clause). If the solution implemented on a small scale failed than you return to the first step: Evaluate or second: Do. If you succeeded progress to the next step. The last step named Act or more precisely Amend. Depending on the results of the change: if they bring improvement, we roll out the change in policies throughout organization, if not, we review the objective and the plan, we find better solutions and repeat E-PDCA cycle (this is part of the Improvement ISO 9001 clause).
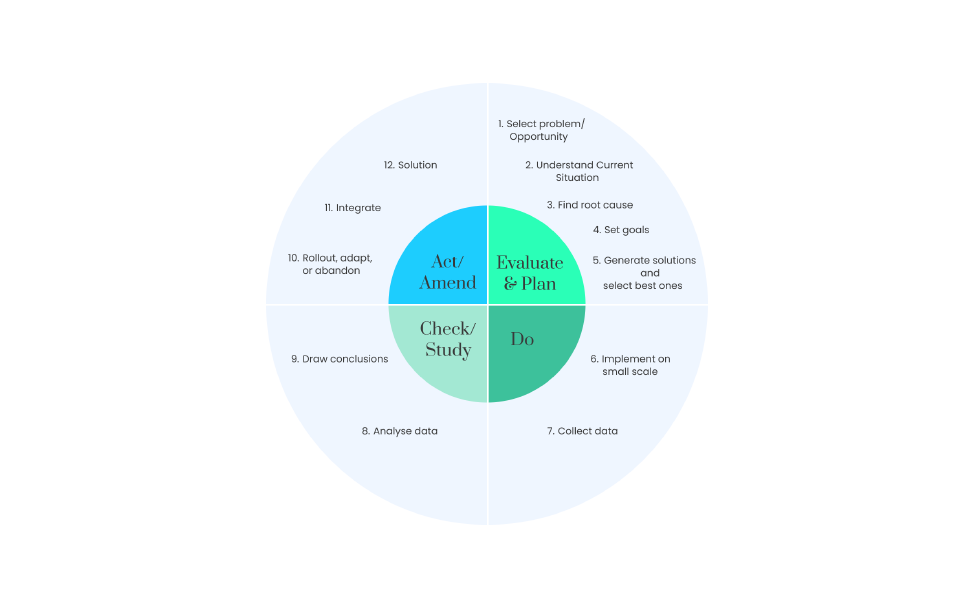
So how we go about making the Quality Management System work in our business? There are 4 phases to help us do it in an orderly and efficient way: Establishment of the system, Implementing the system, Maintaining the system and Improving the quality system.
In the first phase we approach the organization from a systems perspective and we put a boundary around the elements that through their interactions create and retain customers, and put all other elements outside the controlled system. We map the processes and create a library for them. We create a model with systems maps, process maps, activity sequence diagrams and organization charts. You can also include the key issues from the SWOT analysis relative to the processes.
Second phase is implementing the quality system. We put into effect any new policies and practices and introduce change management methods. The most important elements of this change include: obtain the management and employee commitment, appoint the right leader, establish clear rule for communication, prioritize action, follow the plan and track progress, take responsibility, coordinate, allow sufficient time, deal with the resistance to change, educate and train the staff affected by the change and recognize which goals are unrealistic.
Third phase – managing a quality management system – is key, because any system without maintenance will deteriorate. In maintaining the QMS you will need to keep correcting special causes of variations, keep physical resources operational, keep the personnel competent (capable: knowledge, skills and having resources: tangible assets, intangible assets and human assets) keep financial resources ready to replenish consumables, worn out or obsolete equipment, keep the documented information up to date, keep space available to accommodate input and output, keep buildings, land and offices clean and tidy, remove the waste and keep benchmarking processes against best in the field.
The last, fourth phase deals with continually improving the quality system. This means that we have to be putting into effect changes made to the model on a recurring basis to enhance the performance of the organization. We should understand that we must improve not only the effectiveness of the quality system, but also the quality of our products and services. We should also mention that as the continual improvement is important, the discontinuous improvement is at least same important or more. The discontinuous improvement is tantamount to creativity and transformation.
Continual improvement of the QMS is specifically focused on the attributes of suitability, adequacy and effectiveness.
Continually improving suitability (being right and correct for a particular situation or person) means gradually improving the extent to which the QMS fits the organization's purpose. Continually improving adequacy means gradually improving the extent to which the QMS is sufficient (enough) in meeting the applicable requirements. Continually improving effectiveness (successful in something you want to do) means gradually improving the extent to which planned activities are realised and planned results achieved.
Apart from the continuous improvement method, quality management is based on a process approach. The process is anything that can be described by a verb ending in -ing with preferably an object, for example, ‘making bread’. Apart from continuously improving products or services, the business has to improve their internal processes to achieve cost reductions and more job satisfaction for the employees.
If a process is needed to achieve an objective, we need to resource it and make it operational. We also know that processes require activation, that is, an event that triggers them into operation. To ensure that a predetermined process is run when the event that would activate it occurs, people need to respond to that event. And that to happen they need to be aware that a process has been designed for such an event. This is where a role of process maps and process libraries applies. They show relationships between the processes, inputs and outputs and further description.
It might be useful when running a business operation optimization to determine all most important processes by mapping them. Such processes need to be easily accessible by establishing process libraries. When mapping processes it’s good to establish: the activators: input, event or time; the inputs: work instruction, raw material, tool, measuring method, measuring device, protection, feedback; and outputs: plan, activity record, waste, noise, measurement record, conforming item, nonconforming item, feedback.
Outputs are direct effects produced by a process and further on we encounter outcomes i.e. indirect effects of a process having effects upon other stakeholders. Take into consideration that there are 4 core business processes: mission management, resource management, demand creation and demand fulfilment.
Mission management process determined the purpose, mission and direction (strategy) of the businesses, continually confirms that the business is proceeding in the right direction and makes course corrections to keep the business focused on its mission. The business processes are developed within mission management as the enabling mechanism by which the mission is accomplished.
Resource management process specifies, acquires and maintains the resources required by the business to fulfil the mission and disposes off any resources that are no longer required. Demand creation process identifies new technologies, new markets, unsatisfied customer needs and exploits markets with products and services and a promotional strategy that influences decision makers and attracts potential customers to the organization. New product and service development would form part of this process if the business were market driven.
Demand fulfilment process converts customer requirements into products and services in a manner that satisfies all stakeholders. New product development would form part of this process if the business were order driven (the order contained performance requirements for which a new product or service had to be designed). Each of these processes comprise of further work processes, work processes comprise of activities and activities comprise of tasks. Here are more detailed examples of work processes or activities that are grouped in the following way:
Managing mission: scan external environment, establish vision & mission, develop org structure, identify strategic issues, manage enterprise risk, develop capability, establish goals, develop strategy, measure performance, manage PR; Managing resources: develop HR strategy, plan human resources, manage IT, manage finance, recruit employees, deploy resources, manage assets, maintain buildings, maintain equipment, manage employee relations;
Creating the demand: understand markets, plan product development, develop marketing strategy, advertise product, test market, develop product, build prototypes, receive enquiries, accept orders; Fulfilling the demand: plan production/service, select suppliers, develop production process, produce product, procure materials/services, pack product, assemble & test product, deliver product/service, manage logistics, support customer.
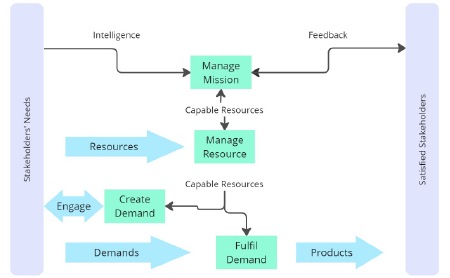
When we undertake work we do it for a reason (past) and to achieve some objective (future). We acquire the things we need to achieve the objective; there is a series of actions we take; tools, equipment and information we use; energy and materials we consume; and decisions we make from the beginning to the end. These are variables. The work progresses until completion. This progression is a process; it has a beginning and an end. It begins with an event or when we receive a command or reach a date and ends when we are satisfied with the resultant output. This output might be a tangible product or a service we provide to someone else. The output will possess certain features or characteristics, some of them needed, some of them not needed.
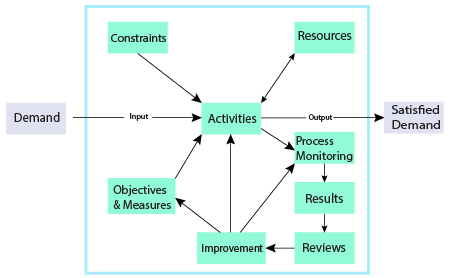
Measures (in the diagram above) are performance measures such as metrics to determine if a target objectives and goals are being met, i.e. productivity, profit margin, cost.
There are 7 aspects of the ISO 9000 quality management standard: Context of organization, Leadership, Planning, Support, Operation, Performance evaluation and Improvement.
In the first aspect called the Context, we focus on our external and internal environment, we try to understand our organization, understand the needs and expectations of interested parties, determine the scope of our quality management system and its processes.
In the Leadership aspect we try to understand the leadership quality and commitment, we draw up the quality policy, determine organizational roles, responsibilities and authorities and focus on customer. In the Planning aspect of the standard we plan actions to address risks and opportunities; and we set up quality objectives.
In the Support aspect we analyse all crucial elements to achieve high quality such as: people, infrastructure, environment for processes, monitoring, measuring resources, organizational knowledge, competence, awareness, communication and documented information.
In the next aspect of the quality standard the Operation, we deal with the operations management area concerned with designing and controlling the processes of designing and producing products and designing and providing services. It covers the demand fulfilment process with interfaces to demand creation, resource management and mission management.
The Performance Evaluation aspect deals with monitoring, measurement, analysis and evaluation, customer satisfaction and management review. And the last aspect of the quality management standard the Improvement helps to determine and select opportunities for improvement, deals with nonconformity, corrective actions and continual improvement of the quality management system.
For an organization to achieve its vision it needs constancy of purpose, and the quality policy is one such artefact to create constancy of purpose relative to quality.
To quickly assess the state of your approach to quality ask your company these quality questions: Do customer receive defective products even if they will accept them? Do employees put quality first and consequently potentially stop the production line?
Is it an environment where employees hide their mistakes or freely own up to them? Is it an environment where employees walk by problems they find or alert the area supervisor? Do employees meet targets changed to align with the process’s assessed capability? Are downstream processes to compensate for the poor quality provided by upstream processes? Do employees tolerate poor performance of materials, equipment, facilities, processes, people or initiate improvement? Quality management system when properly implemented and audited by a certification body can become a very good reputation enhancer and in itself it can motivate staff to be more creative and productive.